Blog Articles
When it comes to selecting the ideal filling solution for your operation, understanding the options available for filling to a level is crucial. At Laub/Hunt, we offer a full range of precision filling systems tailored to your specific product, container, and production goals. Explore the Range of Level Fill Technologies There are several proven methods for achieving a consistent fill level in packaging: Gravity Fill : This is the simplest and most reliable method, ideal for water-thin products. Gravity systems rely on consistent head pressure, ensuring uniform fill levels with minimal maintenance. It’s a cost-effective and efficient choice for many industries. Gravity/Vacuum Fill : A hybrid option that enhances gravity filling by introducing vacuum assistance for more controlled performance in certain applications. Pressure Fill : Designed to handle more viscous liquids, this method applies controlled pressure to achieve fast and accurate fills. It’s perfect for increasing throughput while maintaining quality. Balanced Pressure Fill : By precisely balancing the pressure in both the tank and container, this system is ideal for heavier viscosity products. It improves fill accuracy and boosts overall production efficiency. Balanced Vacuum Fill : A preferred choice for glass containers , this method reduces foaming and product loss by gently drawing liquid into the container via vacuum. It’s a smart solution for delicate packaging needs. Matching the System to Your Product The key to success is choosing the right filling technology based on product characteristics and container type. Our team at Laub/Hunt performs thorough evaluation and testing to ensure each system meets your requirements, whether you're filling beverages, chemicals, cosmetics, or specialty liquids. Why Laub/Hunt? Decades of experience in custom filling systems Engineered solutions for virtually any product or viscosity Proven performance in diverse packaging applications Commitment to accuracy, efficiency, and ease of use Ready to Upgrade Your Filling Line? If you're unsure which system is best for your product or want to optimize your production with accurate and efficient level filling, we're here to help. Contact Laub/Hunt today for a personalized consultation and discover how our engineered filling solutions can elevate your operation. 👉 Request a Quote or Schedule a Consultation Now
As technology evolves, so does bottle filling equipment . Manufacturers are embracing smarter, faster, and greener solutions to keep up with demand and environmental standards. Here’s what the future holds. Increased Automation and Smart Controls Expect greater use of IoT and AI in bottling systems. Smart sensors will optimize fill levels, detect anomalies, and allow for remote diagnostics—reducing human intervention and downtime. Sustainability-Driven Designs Filling equipment is moving toward eco-friendly operation . Expect machines that reduce water usage, minimize product waste, and support recyclable packaging materials. Flexible Fill Capabilities As brands diversify product lines, machines need to handle a range of viscosities and bottle types. Multi-function fillers that accommodate liquid, semi-liquid, and foamy products are on the rise. Compact and Modular Systems Smaller manufacturers and startups need space-saving, modular filling equipment that grows with their production demands. These plug-and-play systems are the future of scalable bottling. Predictive Maintenance Advanced equipment will include predictive maintenance features , alerting operators to potential issues before they become costly breakdowns. Stay Ahead of the Curve with Laub/Hunt At Laub/Hunt , we stay on top of industry innovations to deliver forward-thinking solutions. Whether you’re upgrading or planning for future growth, we’ve got the technology to future-proof your bottling line. 👉 Reach out today and explore how we can help you stay competitive. Keywords: future of bottle filling equipment, automated bottling trends, smart filling machines, sustainable packaging solutions, AI in manufacturing
In today's fast-paced production environments, integrating bottle filling equipment with packaging lines is no longer a luxury—it’s a necessity. Seamless integration ensures smoother workflows, higher efficiency, and better product consistency across all stages of bottling and packaging. Benefits of Integration Increased Efficiency: When bottle filling systems are synchronized with conveyors, cappers, labelers, and cartoners, production flows without interruption. Reduced Downtime: Integrated systems communicate in real time, reducing bottlenecks and minimizing manual adjustments. Consistent Quality: Automation maintains fill levels, eliminates spillage, and ensures uniform product presentation. Key Considerations for Integration Compatibility: Equipment should be modular or customizable to adapt to varying container types, fill volumes, and production speeds. Control Systems: Unified control panels and PLCs streamline management and monitoring. Maintenance and Upkeep: Centralized systems simplify maintenance schedules and troubleshooting. Applications Across Industries From food and beverage to pharmaceuticals , cosmetics , and chemical manufacturing , every industry can benefit from an integrated approach. Whether you're bottling water, essential oils, or hand sanitizer, integrating equipment streamlines your entire operation. Optimize Your Bottling Line Today At Laub/Hunt , we specialize in designing and supplying bottle filling equipment built for integration. Let us help you boost productivity and streamline your operations. 👉 Contact us now to discuss your filling and packaging needs. Keywords: bottle filling equipment, packaging line integration, automated bottling systems, fill and pack solutions, production line efficiency
Precision, speed, and consistency are essential for success with regards to bottle filling. Whether you’re in the food, beverage, pharmaceutical, or chemical industry, ensuring each product is filled accurately is critical. One of the best solutions for achieving this is a Pressure Metering Filler , a system designed to deliver precise and consistent fills using controlled pressure. If you are looking for a way to enhance your filling line’s performance, check out the Pressure Metering Filler available from Laub Hunt, built for accuracy and efficiency. A Pressure Metering Filler works by using positive pressure to meter liquid products directly into containers. Unlike gravity-fed or volumetric fillers, pressure metering fillers allow for a higher degree of control, making them ideal for handling a wide range of liquid viscosities. This type of filling system is perfect for companies that require dependable accuracy, especially when product consistency is vital for quality control. You can explore the full details and features of Laub Hunt’s Pressure Metering Filler to learn how it can benefit your production process. Among the top benefits of using a Pressure Metering Filler is its ability to maintain high accuracy for a variety of liquid products, from thin liquids like water to thick substances like syrups, gels, or sauces. By ensuring each container is filled to the exact required level, manufacturers can avoid costly product waste due to overfilling and minimize rework from underfills. This accuracy translates directly into higher profits and better customer satisfaction. Another key advantage is the increase in production efficiency. Laub Hunt’s Pressure Metering Filler is designed to maintain a consistent fill rate, enabling manufacturers to produce more units in less time without sacrificing quality. This system also offers a hygienic and sanitary design, making it especially suitable for industries like food, beverage, cosmetics, and pharmaceuticals where cleanliness is essential. Easy-to-clean components and smooth surfaces ensure that product changeovers and sanitation processes are quick and efficient. Customization is another reason many companies turn to Laub Hunt for filling solutions. The Pressure Metering Filler can be tailored to match a wide variety of container types, liquid viscosities, and production line requirements. Whether you are working with bottles, jars, or specialized packaging, this filler adapts to meet your needs, making it a versatile choice for growing businesses. Industries that benefit from pressure metering fillers include food and beverage companies filling sauces, juices, dairy, and oils, pharmaceutical manufacturers handling syrups and liquid medications, cosmetic companies producing lotions, creams, and shampoos, and chemical industries working with cleaning agents and industrial liquids. For all these sectors, investing in a Pressure Metering Filler means more consistent products and greater production reliability. Choosing Laub Hunt’s Pressure Metering Filler means investing in quality engineering, personalized service, and long-term performance. Their systems are built to integrate seamlessly into existing lines and come with expert support to help optimize every stage of your filling process. If you're ready to improve your filling line with a Pressure Metering Filler , visit laubhunt.com to learn more and contact their team for a customized solution that fits your specific production needs.
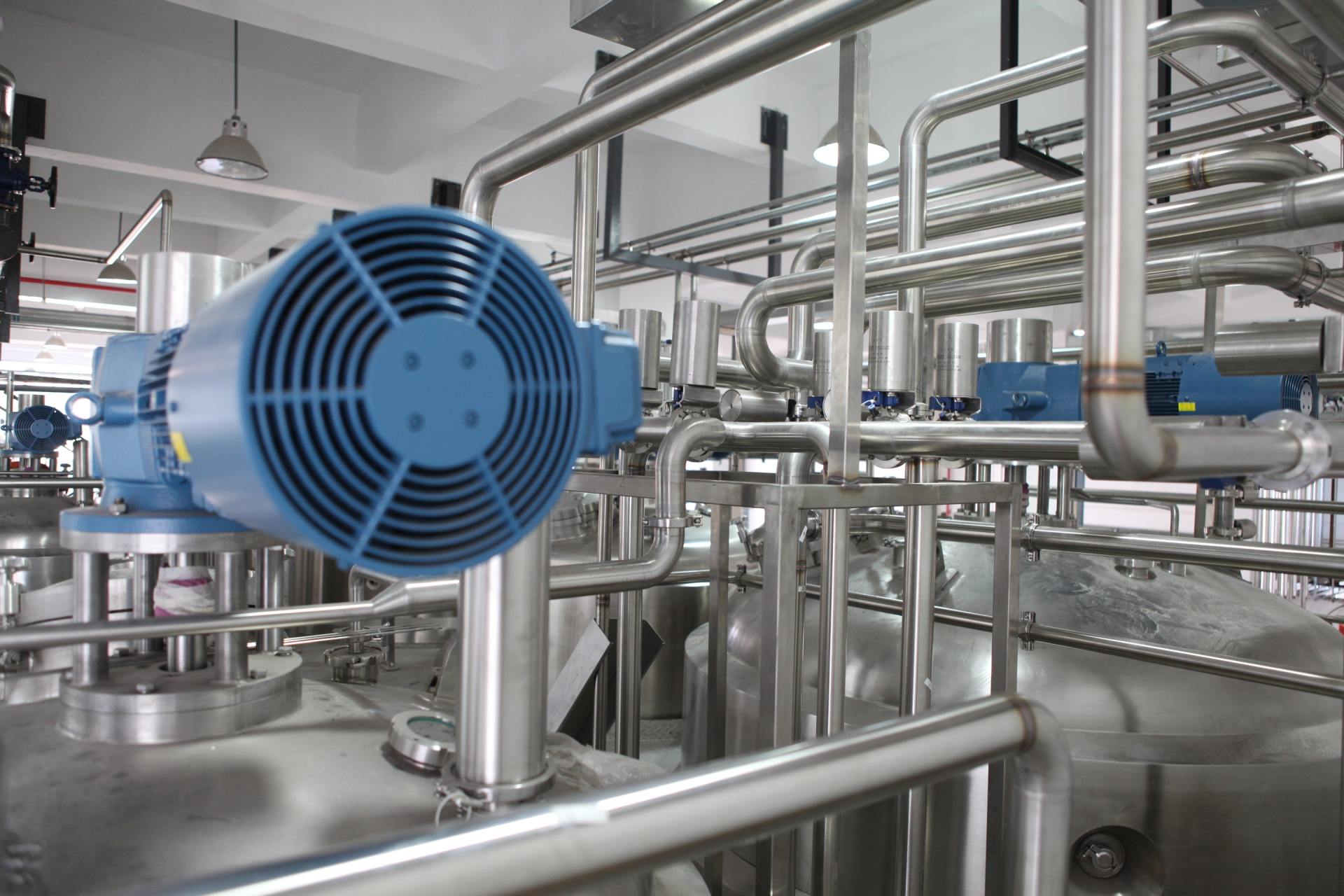
Selecting the appropriate bottle filler is crucial for optimizing your production line's efficiency and ensuring product quality. At Laub/Hunt , we offer four distinct types of bottle fillers, each designed to meet specific production needs. Rotary Mag-Flow Filler Our Rotary Mag-Flow Filler utilizes electromagnetic flow meter technology to achieve precise and accurate filling. This system is ideal for the beverage industry, ensuring consistent fill volumes for products like juices, water, and other non-carbonated drinks. The rotary design enables high-speed operations, making it suitable for large-scale production lines. Key Features: High Precision: Magnetic flow meters provide accurate measurement of liquid flow rates. High-Speed Operation: Rotary mechanism allows for efficient filling at high speeds. Versatility: Suitable for a wide range of liquid products. Pressure Metering Filler Designed for high-viscosity and semi-liquid products, the Pressure Metering Filler employs a positive displacement pump to maintain consistent pressure, ensuring uniform fills. This filler is perfect for products like sauces, creams, and other thick substances. Its sanitary design includes stainless steel construction and Clean-In-Place (CIP) systems, facilitating easy cleaning and maintenance. Key Features: Accurate Filling: Achieves fill accuracies of +/- 0.5%. Sanitary Design: Stainless steel construction suitable for food and cosmetic products. Versatility: Handles a wide range of high-viscosity products. Rotary Volumetric Filler The Rotary Volumetric Filler operates on a positive displacement principle, ensuring each container receives an exact volume of product. This system is beneficial for products where precise volume is critical, such as in pharmaceuticals or specialty chemicals. The enclosed design prevents air from entering the system, maintaining product integrity and reducing oxidation. l Key Features: Precision: Delivers exact volumes for each fill. Enclosed System: Prevents contamination and maintains product quality. Adaptability: Suitable for various liquid viscosities. Rotary Liquid Filler Our Rotary Liquid Filler offers multiple filling methods, including gravity, pressure, and vacuum systems, to accommodate different product characteristics. This flexibility makes it ideal for a diverse range of products, from thin liquids like water to more viscous substances. The machine's design ensures high-speed filling with fill accuracy of +/- 1/16 inch, enhancing both efficiency and precision. Key Features: Multiple Filling Methods: Customizable to product-specific requirements. High-Speed Filling: Capable of speeds up to 1,000 containers per minute. Precision: Ensures consistent fill levels across all containers. Choosing the right bottle filler depends on factors such as product viscosity, desired fill speed, and specific industry requirements. At Laub/Hunt , we are committed to providing tailored solutions that meet your unique production needs. Explore Our Filling Solutions Visit our Fillers page to learn more about each of our bottle fillers. Our team of experts is ready to assist you in selecting the perfect equipment to enhance your production line's efficiency and product quality. Contact Us Today For personalized assistance and to request a quote, contact us . Let Laub/Hunt be your partner in achieving optimal filling solutions for your business.
In the beverage, pharmaceutical, and personal care industries, optimizing your production line for efficiency and profitability is critical. Investing in advanced bottle filling machinery can significantly improve throughput, reduce product waste, and lower operational costs, leading to a strong return on investment (ROI). Whether you're a small business scaling up production or a large manufacturer looking to enhance efficiency, choosing the right bottle filling machine can make all the difference. The ROI of Upgrading to Advanced Bottle Filling Machines 1. Increased Production Speed Modern bottle filling machines can process thousands of bottles per hour, far outpacing manual or semi-automated systems. Faster production speeds mean higher output, which translates to greater revenue potential. 2. Reduced Product Waste Precision is key in liquid filling. Advanced machinery from Laub/Hunt ensures accurate fill levels, minimizing product loss due to spillage or overfilling. Over time, these savings contribute to a higher ROI. 3. Lower Labor Costs Automation reduces the need for manual labor, allowing businesses to operate efficiently with a smaller workforce. This cost reduction improves profit margins and allows employees to focus on quality control and other value-added tasks. 4. Versatility and Adaptability Investing in a machine that can handle different bottle sizes, cap types, and viscosities can future-proof your production line. Laub/Hunt offers versatile bottle filling solutions designed to adapt to evolving market demands. 5. Enhanced Product Quality and Consistency Uniform fill levels and reduced contamination risks contribute to improved product quality, which enhances brand reputation and customer satisfaction. Choosing the Right Bottle Filling Machinery When selecting the best bottle filling equipment, consider the following factors: Type of Liquid: Viscosity, foaming properties, and particulate content determine the type of filler needed. Production Volume: High-speed automated fillers are ideal for large-scale operations, while smaller businesses may benefit from semi-automatic solutions. Container Type and Size: Machines should accommodate the range of bottles used in your product line. Regulatory Compliance: Ensure your equipment meets industry standards, particularly in the food, beverage, and pharmaceutical industries. Explore Laub/Hunt's Bottle Filling Machines to find the right fit for your production needs. Optimize Your Production Today Upgrading to an advanced bottle filling machine is a strategic investment that maximizes efficiency, reduces costs, and ensures consistent product quality. At Laub/Hunt, we specialize in providing high-performance filling solutions tailored to your industry's specific requirements. Ready to enhance your bottling process and boost your ROI? Contact Laub/Hunt today to discuss your production needs and discover the best solution for your business.
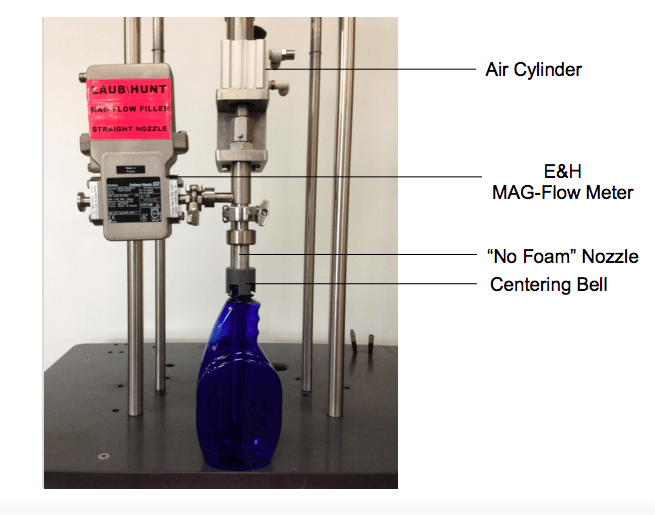
Bottle filling technology plays a crucial role in the beverage, pharmaceutical, cosmetic, and food industries. Selecting the right bottle filling machine is essential for maximizing efficiency, maintaining product integrity, and meeting industry regulations. Understanding the different types of bottle filling technologies can help manufacturers choose the best solution for their production needs. Overflow Fillers Overflow fillers are commonly used for filling bottles with liquid products such as juices, sauces, and cosmetics. These machines ensure a consistent fill level, making them ideal for transparent bottles where visual appeal is important. The overflow filling process allows excess liquid to be recirculated, reducing product waste. Gravity Fillers Gravity filling machines are best suited for thin, free-flowing liquids like water, vinegar, and alcoholic beverages. These machines rely on gravity to dispense the liquid into the bottle. Their simple design makes them cost-effective and easy to maintain, making them a preferred choice for small to medium-scale production. Piston Fillers Piston fillers are ideal for thicker liquids such as honey, syrups, lotions, and pastes. They use a piston mechanism to dispense a precise volume of product into each bottle, ensuring accuracy and reducing product loss. These machines are available in both semi-automatic and fully automatic configurations to accommodate different production scales. Pump Fillers Pump filling machines are designed for products with varying viscosities, from thin to thick liquids. These machines use positive displacement pumps to control the amount of liquid dispensed. They are particularly effective for handling foamy or thick products such as detergents, creams, and oils. Net Weight Fillers For industries that require precise weight-based filling, net weight fillers are the best choice. These machines ensure each bottle contains an exact amount of liquid by measuring its weight during the filling process. They are commonly used in the chemical and pharmaceutical industries where accuracy is paramount. Vacuum Fillers Vacuum filling machines work by removing air from the bottle before dispensing liquid. This technology is often used for filling glass bottles with perfumes, essential oils, and specialty beverages. Vacuum fillers help prevent oxidation and maintain the product's quality over time. Choosing the Right Bottle Filling Machine Selecting the right bottle filling machine depends on various factors, including the type of liquid, production speed, bottle size, and industry requirements. Automated bottle fillers enhance efficiency, reduce labor costs, and ensure consistency, making them a valuable investment for manufacturers. At Laub/Hunt, we offer a wide range of bottle filling solutions designed to meet the diverse needs of different industries. Whether you need an overflow filler, gravity filler, piston filler, pump filler, net weight filler, or vacuum filler, our experts can help you find the perfect solution for your production line. Get Started with the Best Bottle Filling Technology Enhance your production efficiency with high-quality bottle filling machines from Laub/Hunt. Explore our advanced bottle filling solutions and find the perfect fit for your needs. Contact us today to discuss your requirements and optimize your bottling process!
Small to medium enterprises (SMEs) are continually looking for ways to enhance efficiency and streamline operations. For businesses in industries such as food and beverage, pharmaceuticals, cosmetics, and more, innovative bottle filling solutions play a crucial role in meeting production goals without breaking the bank. At Laub/Hunt , we specialize in offering state-of-the-art, customizable bottle filling machines tailored specifically to the needs of SMEs. Why SMEs Need Advanced Bottle Filling Solutions Scalability SMEs often experience fluctuations in demand and need equipment that can adapt to their growing production needs. Laub/Hunt offers bottle filling solutions that are scalable, ensuring businesses can easily adjust to increasing orders without the need for costly upgrades. Cost-Effectiveness Operating on a budget doesn’t mean sacrificing quality. Our equipment is designed to provide maximum output while minimizing operational costs. By using energy-efficient technologies and reducing product waste, our systems deliver a higher return on investment. Customization Unlike off-the-shelf solutions, Laub/Hunt bottle filling machines are highly customizable. Whether you need equipment for specific bottle shapes, unique product viscosities, or rapid production cycles, we tailor our systems to your exact specifications. Ease of Use For SMEs with smaller teams, simplicity is key. Our machines are designed for intuitive operation, with minimal training required. User-friendly controls and low-maintenance designs help businesses save time and reduce downtime. Benefits of Choosing Laub/Hunt Bottle Filling Solutions Precision Filling: Advanced technology ensures accurate and consistent fills for every bottle. Versatility: Suitable for a variety of products, including liquids, gels, and semi-solids. Compliance: Adheres to industry standards and regulatory requirements for safety and hygiene. Durability: Built to last with high-quality materials, ensuring long-term reliability. Industries We Serve Laub/Hunt has a proven track record of working with SMEs across a wide range of industries: Food and Beverage: From sauces and syrups to juices and oils, our systems handle a diverse array of products. Pharmaceuticals: Precise filling for medicines, supplements, and other health products. Cosmetics and Personal Care: Streamline production for lotions, shampoos, and skincare products. Chemical Products: Safely and efficiently fill cleaning solutions, detergents, and more. If your SME is ready to take production to the next level with innovative, reliable, and cost-effective bottle filling solutions , Laub/Hunt is here to help. Our team of experts is dedicated to finding the perfect equipment for your business needs. Contact Laub/Hunt today to discuss your requirements and discover how our bottle filling machines can revolutionize your operations. With Laub/Hunt, innovation meets efficiency, empowering your business to thrive in a competitive marketplace. Don’t wait—upgrade your bottle filling process today!
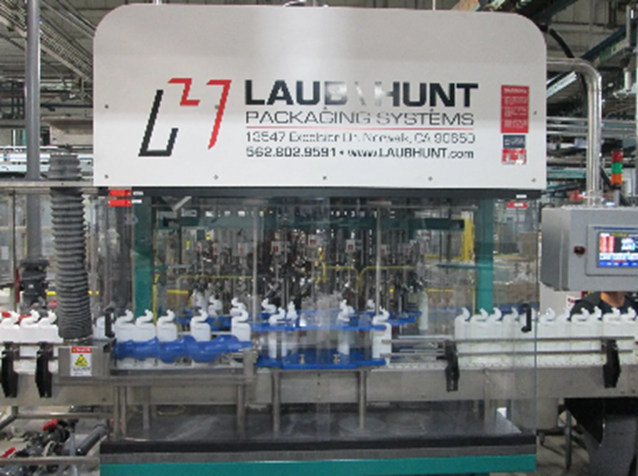
In industries where precision and efficiency are critical, the Rotary Volumetric Filler from Laub\Hunt stands out as a game-changing solution. Designed for seamless integration into your production line, this advanced filling equipment offers unparalleled accuracy, speed, and reliability for businesses across the food, beverage, and chemical industries. At the heart of the Rotary Volumetric Filler is its ability to handle a variety of liquids with precision. Whether you’re working with thin, free-flowing products or thick, viscous liquids, this machine ensures consistent and accurate fills every time. Its rotary design allows for continuous operation, boosting productivity without sacrificing quality. Built with robust materials and advanced technology, the Rotary Volumetric Filler is engineered for longevity and low maintenance. Its user-friendly interface makes it easy to operate, reducing training time and minimizing production downtime. Customizable options allow businesses to tailor the machine to their specific needs, ensuring maximum efficiency and flexibility. Safety and hygiene are key priorities in today’s manufacturing environment, and Laub\Hunt delivers on both fronts. The Rotary Volumetric Filler is designed to meet stringent industry standards, with features that promote cleanliness and operational safety, giving you peace of mind in every aspect of your production process. Investing in the Rotary Volumetric Filler means elevating your business operations to new heights of efficiency and reliability. Whether you’re looking to enhance your existing production line or expand your capabilities, this machine offers the perfect balance of performance and value. Contact Laub\Hunt today to learn more about the Rotary Volumetric Filler and how it can revolutionize your production process. Let Laub/Hunt provide the innovative solutions your business needs to succeed.
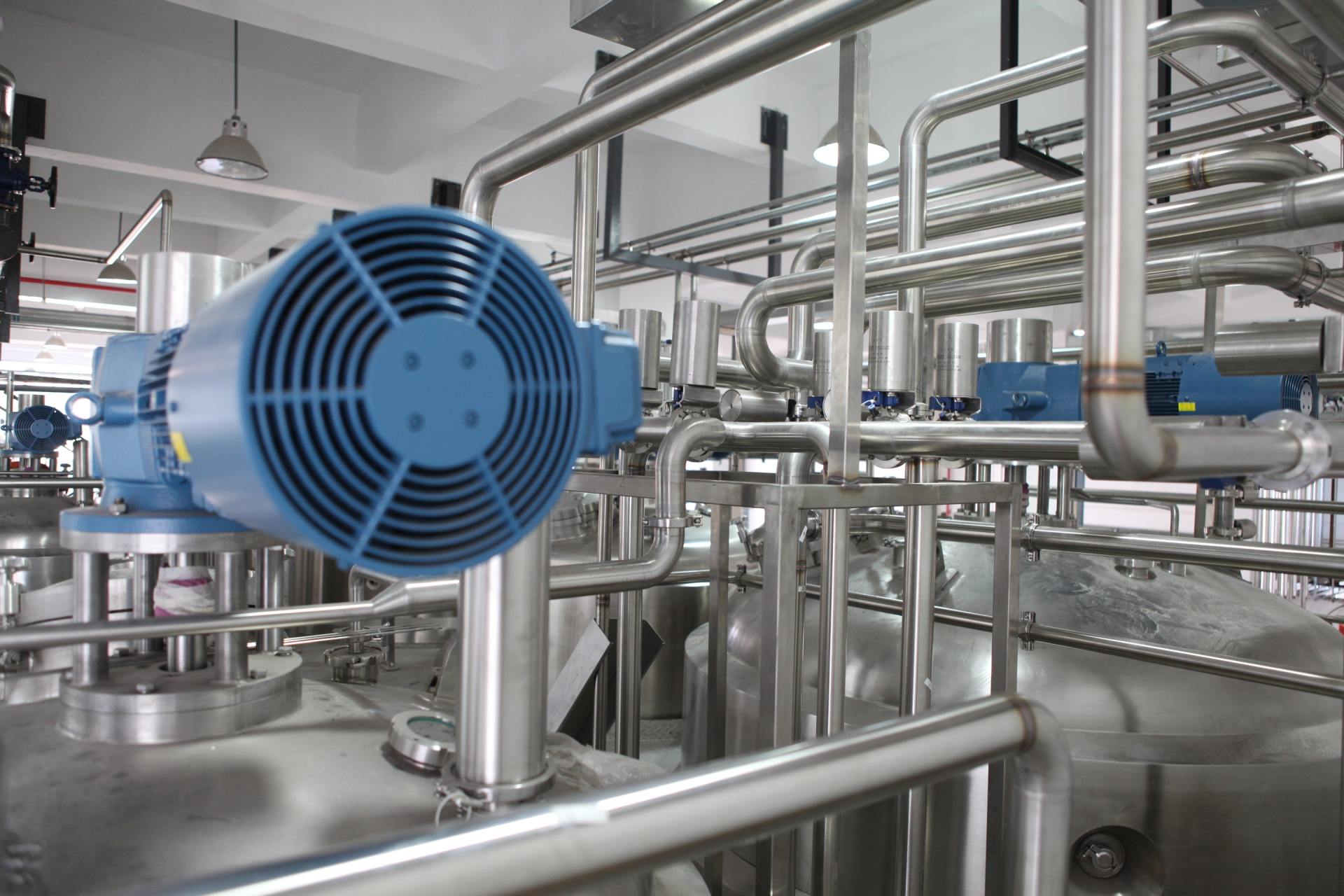
At Laub\Hunt, we specialize in delivering innovative engineering solutions for liquid filling equipment and production lines. With a global reputation for reliability and precision, we offer services that ensure your operations run efficiently and effectively. From turn-key project management to technical support and field services, our team is here to support your machinery needs at every stage of the process. Expertise in Liquid Filling Equipment Solutions LAUB\HUNT is your trusted partner for complete production line integration. Whether you're starting a new project or upgrading existing equipment, we offer a wide range of services tailored to meet your specific requirements: Engineering for Line Integration: Our team designs and implements liquid filling systems that seamlessly integrate with your production lines for optimal performance. Turn-Key Project Management: We manage every phase of your project, from initial planning and design to installation and commissioning, ensuring a smooth and stress-free process. Start-Up and Commissioning Services: Our field technicians provide on-site assistance to ensure your equipment is operational and performing to specification. Troubleshooting and Upgrades: Address challenges quickly and efficiently with our expert technical support, or enhance your system’s capabilities with our upgrade services. Rebuilding and Maintenance: Restore and extend the life of your liquid filling equipment with our rebuilding solutions, designed to keep your machinery in peak condition. Global Reach, Tailored Expertise With clients around the world, Laub\Hunt brings a unique combination of global experience and industry-specific expertise to every project. Our solutions are customized to fit the needs of businesses across various sectors, ensuring you receive the right support no matter your location or production scale. Standing Behind Every Solution At Laub\Hunt, quality and customer satisfaction are at the heart of everything we do. We take pride in offering dependable solutions and standing behind our products and services. This unwavering commitment to excellence has made us a leader in the liquid filling equipment industry, trusted by businesses globally. Let LAUB\HUNT Elevate Your Operations Choose LAUB\HUNT for comprehensive engineering services that drive efficiency and innovation in liquid filling equipment solutions. From concept to completion, our team ensures your production line operates seamlessly. Contact us today to discuss your project or learn more about our range of services. Let LAUB\HUNT be your global partner in liquid filling equipment success. Transform your liquid filling operations with Laub\Hunt—where expertise meets innovation.