Safety Features to Look for in Modern Bottle Filling Equipment
Safety Features to Look for in Modern Bottle Filling Equipment
In today’s fast-paced food and beverage industry, maintaining safety during bottling operations is crucial. Modern bottle filling equipment integrates advanced safety features that protect workers, maintain product quality, and minimize downtime. Whether you're upgrading your equipment or expanding operations, understanding these features ensures that your production line runs smoothly and safely.
Key Safety Features to Consider:
Safety Guards and Interlocks
Modern bottle filling machines come equipped with protective guards and interlocks to prevent accidental access to hazardous areas during operation. These barriers help safeguard workers from moving parts and high-pressure systems.
Emergency Stop Buttons
Strategically placed emergency stop buttons are critical for shutting down operations quickly in case of an issue. They minimize risks by allowing operators to halt the machine instantly to prevent accidents or product contamination.
Automatic Overload Protection
Bottle filling machines with overload protection systems can detect excessive load or pressure, preventing mechanical failures and reducing the chance of injury.
Hygienic Design for Safety and Compliance
A well-designed bottle filling machine ensures compliance with food safety standards by preventing microbial growth and contamination. Look for equipment with stainless steel construction, easy-to-clean surfaces, and CIP (Clean-in-Place) technology.
Non-Slip Surfaces and Stable Footing
The stability of the machine minimizes operational hazards. Machines with non-slip surfaces and adjustable feet ensure the equipment remains secure during operation, preventing slips, trips, or falls.
Integrated Sensor Technology
Sensors monitor various parameters, including pressure, temperature, and fill levels. If abnormalities are detected, the machine automatically stops to prevent equipment damage and maintain product quality.
User-Friendly Control Panels with Alerts
Modern filling machines feature intuitive control panels with visual or audible alerts, warning operators of potential issues like blocked nozzles or low fluid levels. This improves operational safety by providing timely information.
Anti-Drip Nozzles and Precise Filling
Anti-drip nozzles prevent spills and reduce the chances of slips around the machine. Precise filling technology also minimizes waste and ensures accurate dosing.
Compressed Air Monitoring Systems
Monitoring compressed air flow ensures that pneumatic components work safely and efficiently, reducing the risk of operational failure.
Overheat and Pressure Regulation
Temperature and pressure sensors protect operators by preventing overheating or over-pressurization. These features are critical for hot-fill processes or high-pressure carbonated beverage filling.
Safety Certifications and Compliance
Always look for equipment that complies with industry safety standards such as CE, ISO, or OSHA. Certified machines ensure you meet regulatory requirements and industry best practices.
Training Programs for Operators
Many manufacturers offer operator safety training, helping staff understand the machine’s safety protocols, which reduces the likelihood of accidents and boosts efficiency.
Automatic Lubrication Systems
These systems keep moving parts properly lubricated, reducing mechanical failure and minimizing the need for risky manual maintenance.
Remote Monitoring and Diagnostics
Many modern bottle filling machines offer remote monitoring, allowing operators to detect potential issues from a distance. This feature reduces exposure to hazardous areas and facilitates quick troubleshooting.
The Benefits of Safety-Focused Equipment
- Reduced Downtime: Fewer accidents and equipment failures translate to uninterrupted production.
- Regulatory Compliance: Meeting safety standards helps avoid fines and legal issues.
- Improved Employee Morale: A safe working environment boosts employee satisfaction and reduces turnover.
- Enhanced Product Quality: Safety features help maintain hygiene and prevent contamination, ensuring consistent product quality.
- Cost Savings: Preventing accidents and equipment breakdowns reduces maintenance and insurance costs over time.
Ensure Your Bottling Line Runs Safely and Smoothly
Investing in modern bottle filling equipment with advanced safety features is a smart move for any beverage or food business. It not only keeps your workforce safe but also ensures your production line operates efficiently and meets regulatory standards.
Need help selecting the safest and most efficient bottle filling equipment for your business? Contact us today to explore our range of high-quality, safety-compliant bottling solutions!
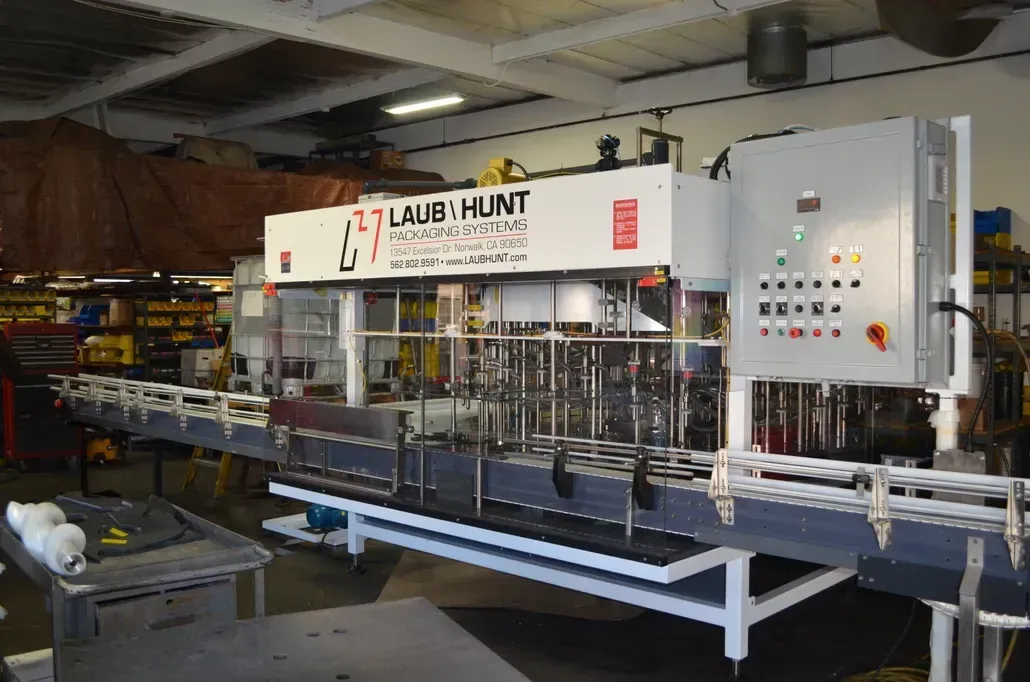